Optimizing VRF System Performance Through Proper Commissioning
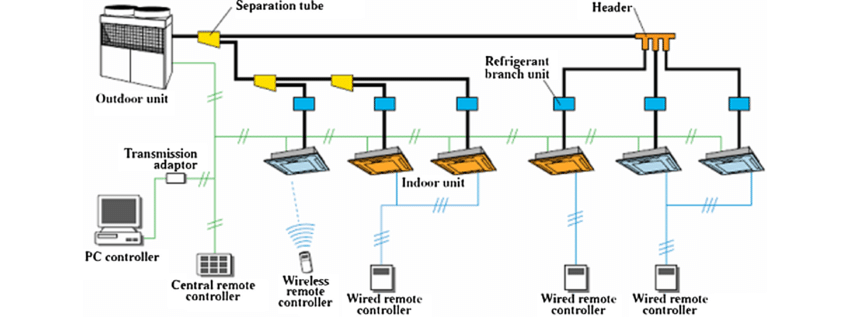
Variable Refrigerant Flow (VRF) systems from leading brands such as Samsung, LG, Daikin, Midea, Gree, Toshiba, Hitachi, Trane and Carrier have become a game-changer in the HVAC industry. Known for their energy efficiency, zoning capabilities, and ability to deliver tailored comfort, these systems are increasingly used in modern buildings. However, their advanced design and unique requirements make proper VRF testing and commissioning absolutely essential.
Unlike traditional HVAC systems, VRF and VRV systems are complex, with precise refrigerant management, intricate piping, and integrated control systems. Many contractors are still adapting to the technical demands of systems from these renowned brands, which heightens the importance of rigorous commissioning. This article highlights the key risks in VRF system installation and explains why thorough testing and commissioning are indispensable for reliable operation.
Why Proper Testing and Commissioning Matter
Testing and commissioning are not just procedural steps—they are critical to ensuring that a VRF system functions as intended. Without them, even minor errors during installation can lead to:
- Poor system performance
- Reduced energy efficiency
- Premature component failures
- Costly repairs and downtime
For VRF systems, commissioning serves as the final quality assurance step to verify that every component, from refrigerant piping to controls, is installed and calibrated correctly. This ensures the system operates safely, efficiently, and according to the manufacturer’s design specifications.
Common Risks in VRF System Installation
The complexity of VRF systems means that certain aspects of their installation require special attention:
- Refrigerant piping design and installation
- VRF systems rely heavily on accurate refrigerant piping. Mistakes in pipe sizing, orientation or routing can disrupt refrigerant flow, leading to inefficiencies or complete system failures.
- Unstable electric power
- Most contractors use electric power generator during the installation process of VRF system, it’s very important to verify the stability and power quality of power supply before running the systems.
- Y-Joint Installation
- Y-joints must be installed correctly to ensure balanced refrigerant distribution. Incorrect placement or orientation can result in uneven heating or cooling across the system.
- Refrigerant Charging
- VRF systems often require precise refrigerant charging, especially for longer piping routes. Overcharging or undercharging the system can severely affect performance and reliability.
- Nitrogen Use During Brazing
- Introducing nitrogen during brazing prevents oxidation inside the pipes. Failure to follow this practice can lead to blockages, EEV failures and reduced system efficiency.
- Deep Vacuuming
- Proper vacuuming removes moisture and air from the system. Skipping or inadequately performing this step can result in internal corrosion and compromised compressor performance.
- Outdoor Unit Placement and Spacing
- Outdoor units must adhere to strict spacing and placement guidelines to allow for proper airflow and heat exchange. Non-compliance can cause overheating and reduced efficiency.
Control System Integration and Programming
VRF systems are highly customizable, requiring careful integration with control systems. Key considerations include:
- Custom Programming for Indoor Units
- Indoor fan speeds must be programmed to suit the specific requirements of each zone, ensuring consistent comfort.
- Sensor Calibration
- The placement and configuration of temperature sensors are critical. Misaligned sensors can result in inaccurate temperature readings, affecting the overall system performance.
- Control System Setup
- Proper integration with building management systems (BMS) ensures seamless operation and monitoring.
The Importance of following Manufacturer Guidelines and Using Service Software
Manufacturer installation and operation manuals are indispensable when commissioning a VRF system. They provide detailed instructions on installation, refrigerant charging, and control programming. Strict adherence to these guidelines ensures the system meets performance expectations.
Additionally, using manufacturer-specific service software during testing and commissioning is vital. This software provides:
- Real-time diagnostics to identify faults
- Tools for optimizing system settings
- Accurate validation of refrigerant and system performance
Without these tools, it is nearly impossible to confirm that a VRF system is functioning at its best.
Steps in VRF Testing and Commissioning
- Pressure and Leak Testing
- Verifies the integrity of refrigerant piping and ensures no leaks are present.
- Refrigerant Charging Verification
- Confirms the refrigerant charge is accurate, accounting for additional requirements based on piping length.
- Vacuuming
- Removes air and moisture from the system, ensuring optimal refrigerant flow and preventing damage.
- Control System Configuration
- Programs fan speeds, calibrates sensors, and integrates the VRF system with the building’s management system.
- Performance Testing
- Uses service software to validate operational parameters and fine-tune the system for peak performance.
- Documentation
- Records all tests, settings, and performance metrics for future reference.
Benefits of Proper Testing and Commissioning
- Enhanced Efficiency: Ensures the system operates at optimal energy efficiency.
- Improved Reliability: Reduces the risk of malfunctions or breakdowns.
- Longer Equipment Lifespan: Protects components from premature wear and tear.
- Cost Savings: Minimizes repair and operational costs through early detection of potential issues.
- Consistent Comfort: Provides precise and reliable heating and cooling across all zones.
Conclusion
Proper testing and commissioning are essential for the successful operation of VRF systems. With their advanced technology and unique installation requirements, these systems demand meticulous attention to detail. From refrigerant piping and Y-joints to control system integration, every step must be performed according to manufacturer guidelines and validated through rigorous testing.
At HVAC MasterLabs, we specialize in VRF system testing and commissioning in UAE, ensuring your system delivers the performance and reliability it was designed for. Whether it’s a new installation or an existing system in need of optimization, our expertise and advanced tools make all the difference.
Contact us today to learn more about our VRF testing and commissioning services.